Iron Rods - Types, Uses, Prices And Manufacturing Process
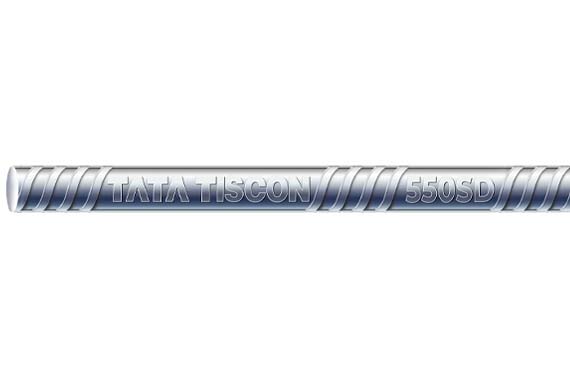
Tata Tiscon 550 sd today price list
Iron rods are used in the construction of buildings, bridges and other infrastructures. Iron rods are strong and sturdy and help to reinforce the concrete structures. These iron rods are made up of steel and are often referred to as rebars.
Different types of iron rods are used in the construction like TMT (Thermo-Mechanically Treated) and HYSD (High Yield Strength Deformed), Galvanised iron rods, MS iron rods, cast iron rods and iron rods powder coated.
The iron rods do not crack under stress and this makes them suitable for structures that face constant wear and tear. The rods are durable and of very high strength and provide stability and resilience to the structures. The iron rods are used in building foundation beams and columns and enable the concrete to bear the heavy load, resist pressure and ensure long-lasting safety.
The rods provide stability and durability to the structures and ensure they can withstand the shock and stress. The rods can also be used in seismic activity and earthquake-prone areas to provide safety and longevity to the buildings.
The price of iron rods in India depends on the type, quality and the market. The prices vary between Rs. 40 to Rs. 60 per kg. Iron rods are a preferred choice in construction because they are also affordable. The Tata tiscon 550 sd today price list as per size is available online. This will help you to get an idea about the costs.
The price of the iron rod is determined by its diameter and length. The grade, dimensions and materials also matter. Other factors are the percentage of iron in iron bars, availability and local market conditions. Different sizes available are 6mm, 8mm,12mm, 16mm and 32mm. The prices of different rods will be different.
Manufacturing process
The manufacturing process involves several steps to ensure strength and quality. The steps are as follows:
- The first step is sourcing and procuring the different raw materials which are scrap iron and iron ore.
- Once the raw materials are prepared they are put into a blast furnace for melting. This process takes place at high temperatures and all the impurities from the raw materials are removed. The result is pure iron metal.
- The molten iron is then refined using a refining furnace. At this stage, the other impurities like sulphur and phosphorous are reduced. This helps to improve the quality and the durability of the iron.
- The purified iron is cast into billets which serve as a base for further processing. The billets can be heated in rolling mills into specific shapes and thicknesses.
- The iron rods produced are cooled (quenched) rapidly and this hardens the outer surface of the rods and maintains high tensile strength.
- After quenching the iron rods are reheated using a process called tempering. This helps to reduce the brittleness in the rods and improves the ductility.
- In the last stage, the rods are cut into the desired length and polished to get a smooth surface finish. Quality checks are performed to ensure standard and consistency.